The Device Chronicle interviews Frederik Arentz Sørensen, R&D engineer, Agrointelli, a company pioneering versatile and autonomous robots solving multiple tasks in the field.
Agrointelli is a pioneer in autonomous robots, autonomous farming and the major brands are looking to do autonomous farming but they do not have the speed and agility of Agrointelli. Also,The company is replacing the driver in the tractor with an autonomous solution which just works for longer and with great precision and accuracy. Frederik is leading the company’s effort to engineer a robust and secure means to keep the robots operational with appropriate software updates.
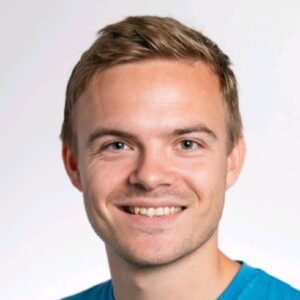
Introducing the ROBOTTI of autonomous robots
Frederik begins the interview by describing Agrointelli’s ROBOTTI solution. The ROBOTTI is equipped with a standard three-point hitch and PTO. This means that the robot can be fitted with standard agricultural implements and perform many different tasks in the field throughout the season.
The robot is autonomously controlled by a computer and does not depend on a human driver. Based on the remote user’s inputs, it calculates and navigates itself and follows an optimized route in the field. The ROBOTTI is equipped with several redundant safety measures.
Equipped with RTK-GPS for precision navigation, the ROBOTTI carries the implement in the center. This means that the weight is evenly distributed on all 4 wheels. Therefore, no weight compensation is needed. The implement does not swing and the robot knows exactly where it is. Therefore, Robotti can operate with incredible accuracy and precision while keeping the overall weight low.
Use cases in autonomous robots in autonomous farming
A variety of different use cases are supported with autonomous farming such as crop spraying, weeding, and planting. The system is already used in large 1000 hectare plus farms in Australia. The system can also handle niche use cases such as working in small fields and terraced fields and there there is flexibility for sowing the field, plowing the field.
Autonomous farming has the obvious benefit of a reduction in labor cost for common agricultural tasks as the Agrointelli system can operate 24/7 and this allows for the redeployment of the farmer and staff to higher level and more productive tasks and projects. The autonomous systems also offer more precise navigation so that the use of water and pesticides can be greatly reduced.
Robots are used in these autonomous farming applications, and the robots are based on embedded systems which require software updates. Mender is used to perform full system updates as a key goal is also to update these embedded systems and to do so without bricking or making these systems non-operational. Frederik says that “It is incredibly important to future proof the device so that new features can easily be added with an OTA update; and that in the absence of a software update roll back mechanism, the robot could fail so an A/B partition for system updates is critical to have in place.” In terms of embedded hardware, the Robotti incorporates a surveillance computer based on the Nvidia Jetson TX2 and a second computer uses a Jetson Xavier.
We wish Frederik and his colleagues well in their mission to bring autonomy to all kinds of agricultural implements and work scenarios.